Case Study: Implementing Automated Visual Inspection in Electronics Manufacturing
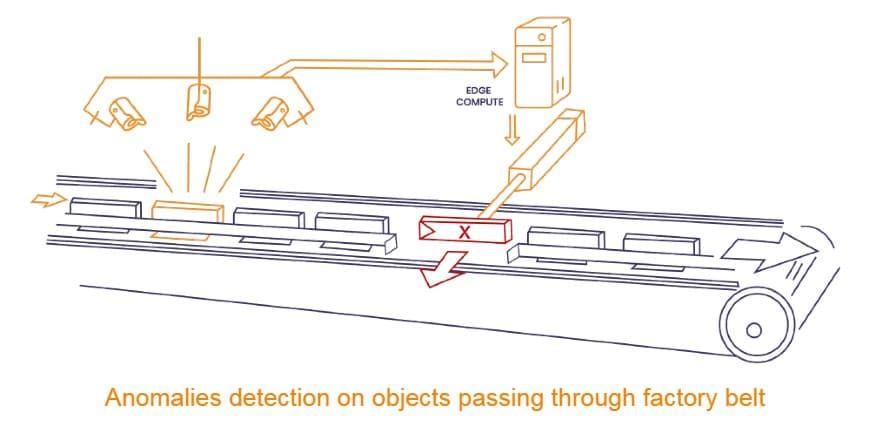
Client Profile
Industry: Manufacturing
Size: Mid-sized contract manufacturer with 500+ employees
Location: North America
Production Volume: 12 million PCB assemblies annually
Our client is a contract electronics manufacturer specializing in printed circuit board (PCB) assembly for automotive, medical, and industrial applications. With stringent quality requirements from their customers and increasingly complex products, they faced significant challenges in maintaining consistent quality standards while meeting production targets.
The Challenge
The client's existing quality control process relied heavily on manual visual inspection, which presented several critical challenges:
- Human Error: Manual inspectors missed approximately 20-30% of defects, resulting in customer complaints and warranty claims.
- Inconsistency: Quality varied significantly between different inspectors and across shifts.
- Throughput Limitations: Manual inspection created bottlenecks in the production process, limiting overall capacity.
- Fatigue: Inspector accuracy declined significantly during long shifts, particularly for fine-detail inspection tasks.
- Rising Complexity: Newer PCB designs with smaller components and higher densities were becoming increasingly difficult to inspect manually.
- Labor Costs: Maintaining a team of trained quality inspectors was becoming increasingly expensive.
The Quality Manager explained their situation: "Our manual inspection process simply couldn't keep up with our production demands while maintaining the quality standards our customers expect. We were facing increasing pressure from both sides – customers wanted higher quality, and production needed faster throughput. Something had to change."
The Solution
After evaluating several options, the company partnered with Visionify to implement a comprehensive Automated Visual Inspection (AVI) system across their production lines:
1. Multi-Stage Inspection System
- High-resolution camera arrays installed at critical inspection points
- Custom lighting setups optimized for different defect types
- Automated handling systems for consistent positioning
- Integration with existing production line equipment
2. AI-Powered Defect Detection
- Deep learning models trained to identify multiple defect categories:
- Component misalignment
- Missing components
- Solder joint defects
- Polarity errors
- Foreign material contamination
- Surface damage
- Continuous learning capability to adapt to new products and defect types
3. Intelligent Classification System
- Multi-tier classification of defects by severity and type
- Customizable acceptance criteria based on product requirements
- Automated sorting of defective units for repair or rejection
- Detailed defect documentation with images and location data
4. Quality Analytics Platform
- Real-time monitoring of defect rates and patterns
- Trend analysis to identify recurring issues
- Production line performance comparisons
- Early warning system for process drift
Implementation Process
The implementation followed a structured approach to ensure minimal disruption to ongoing production:
-
Assessment & Planning (4 weeks)
- Comprehensive analysis of current quality control processes
- Identification of key inspection points and defect types
- Camera and lighting placement planning
- Development of integration strategy with existing systems
-
Data Collection & Model Training (6 weeks)
- Collection of thousands of product images with and without defects
- Annotation of defect types and locations
- Initial model training and validation
- Development of custom algorithms for specific defect detection
-
Pilot Deployment (5 weeks)
- Installation on one production line
- Side-by-side comparison with manual inspection
- System calibration and threshold adjustment
- Initial performance evaluation
-
Full-Scale Implementation (10 weeks)
- Phased rollout across all production lines
- Integration with MES (Manufacturing Execution System)
- Comprehensive training for quality and production staff
- Development of standard operating procedures
-
Optimization & Expansion (Ongoing)
- Regular model updates based on new products and defect patterns
- System refinement based on performance data
- Addition of new inspection capabilities
- Extension to other manufacturing processes
Results
After one year of operation, the Automated Visual Inspection system delivered significant improvements across multiple performance metrics:
Quality Improvements
- 94% reduction in defect escape rates (defects reaching customers)
- 99.7% detection accuracy for critical defects
- 85% reduction in customer quality complaints
- Consistent quality standards across all shifts and production lines
- Early detection of process issues before they affected multiple units
Operational Efficiencies
- 32% increase in production throughput
- 68% reduction in quality control labor costs
- 41% decrease in rework requirements
- 24/7 operation without inspection fatigue or variability
- Faster new product introduction with automated inspection program generation
Financial Impact
- Annual savings of $1.8 million in quality-related costs
- $950,000 reduction in labor expenses
- Increased revenue from higher production capacity
- ROI of 280% within the first year
- Payback period of 4.3 months
Additional Benefits
- Data-Driven Process Improvement: Identification of systematic issues led to upstream process enhancements
- Enhanced Customer Confidence: Detailed inspection data provided to customers increased trust
- Competitive Advantage: Ability to handle higher complexity products at lower costs
- Better Resource Allocation: Quality personnel focused on process improvement rather than routine inspection
- Reduced Environmental Impact: Less waste from defective products
Key Success Factors
Several elements were crucial to the project's success:
-
Hybrid Approach: Combining AI with traditional machine vision techniques for optimal performance.
-
Collaborative Development: Close partnership between Visionify engineers and client quality experts.
-
Phased Implementation: Step-by-step approach that allowed for learning and adjustment.
-
Comprehensive Training: Ensuring all stakeholders understood the system's capabilities and limitations.
-
Continuous Improvement Framework: Regular review and refinement of the system based on performance data.
Implementation Challenges & Solutions
The project faced several challenges during implementation:
-
Product Variability
- Challenge: Wide range of products with different components and layouts
- Solution: Development of flexible models that could adapt to different product types with minimal reconfiguration
-
False Positives
- Challenge: Initial high rate of false defect detections
- Solution: Refinement of detection thresholds and additional training with borderline cases
-
Integration with Legacy Systems
- Challenge: Connecting with older production equipment and databases
- Solution: Development of custom middleware and APIs to bridge technology gaps
-
Staff Adaptation
- Challenge: Initial resistance from quality inspection staff
- Solution: Retraining program that transitioned inspectors to system operators and process improvement roles
Client Testimonial
"Visionify's Automated Visual Inspection system has completely transformed our quality control process. We're now able to inspect 100% of our products with a level of consistency and accuracy that was impossible with manual inspection. The reduction in customer complaints and warranty claims alone justified the investment, but we've also seen significant improvements in production throughput and cost efficiency. The system's ability to learn and adapt to new products has been particularly valuable as our product mix continues to evolve."
— Michael R., Director of Quality
Automated Visual Inspection Technology Overview
Our solution leverages several advanced technologies to provide accurate, high-speed inspection:
Image Acquisition and Processing
- High-resolution industrial cameras capture detailed images of products
- Specialized lighting configurations highlight different defect types
- Multi-angle imaging for comprehensive coverage
- Real-time image processing for immediate analysis
AI-Powered Defect Detection
- Deep learning models trained on thousands of product images
- Convolutional neural networks (CNNs) for visual pattern recognition
- Transfer learning to quickly adapt to new products
- Ensemble approach combining multiple detection methods
Intelligent Classification
- Multi-tier classification system for defect categorization
- Severity assessment based on defect type and location
- Customizable acceptance criteria for different product requirements
- Continuous learning from operator feedback
Analytics and Reporting
- Real-time quality dashboards for production monitoring
- Trend analysis to identify recurring issues
- Defect mapping to pinpoint process problems
- Comprehensive documentation for quality assurance
Advantages Over Manual Inspection
The Automated Visual Inspection system provided several key advantages over traditional manual inspection:
-
Superior Detection Capability
- Higher optical resolution for detecting minute defects
- Consistent inspection criteria applied to every unit
- Detection of defects invisible to the human eye
- Ability to inspect complex, high-density assemblies
-
Increased Speed and Throughput
- Inspection times measured in seconds rather than minutes
- Continuous operation without breaks or shift changes
- Parallel processing of multiple inspection points
- Immediate pass/fail decisions
-
Objective and Consistent Results
- Elimination of subjective judgments
- Consistent application of quality standards
- No degradation in performance due to fatigue
- Detailed documentation of inspection results
-
Data-Driven Insights
- Comprehensive defect statistics
- Pattern recognition across production runs
- Early detection of process drift
- Actionable insights for process improvement
Visionify Solution
Our Automated Visual Inspection solution provided our client with powerful tools to overcome their quality control challenges. Through AI-powered defect detection, comprehensive analytics, and seamless production integration, Visionify not only helped improve product quality but also enhanced production efficiency and reduced costs.
Our client can now confidently deliver high-quality products to their demanding customers while optimizing their manufacturing processes through data-driven insights. This successful implementation exemplifies how Visionify's innovative computer vision solutions can transform manufacturing quality control through advanced AI technology.
Conclusion
This case study demonstrates how Automated Visual Inspection technology can revolutionize quality control in electronics manufacturing. By implementing an AI-powered inspection system, our client was able to significantly improve defect detection accuracy while increasing production throughput and reducing costs.
The success of this implementation has led to the company expanding the use of computer vision technology to other aspects of their manufacturing process, including incoming material inspection and packaging verification. The data collected from the system has also provided valuable insights for process improvements that have further enhanced product quality and production efficiency.
Are you facing similar quality control challenges in your manufacturing operations? Contact Visionify today to learn how our Automated Visual Inspection solutions can transform your approach to product quality and production efficiency.
Ready to achieve similar results?
Let us show you how our Vision AI safety solutions can transform your workplace safety.
Schedule a ConsultationRelated Case Studies
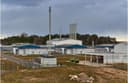
Case Study: How a Multi-Site Industrial Enterprise Leveraged Safety Insights with Visionify's Safety AI Platform
Manufacturing
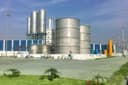
Case Study: How a Global Chemical Manufacturer Transformed Workplace Safety with Visionify's AI Solutions
Manufacturing
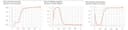
Case Study: How a Leading Irrigation Equipment Manufacturer Enhanced Drilling Precision with Visionify's AI Quality Check Solution
Manufacturing
Schedule a Meeting
Book a personalized demo with our product specialists to see how our AI safety solutions can work for your business.
Choose a convenient time
Select from available slots in your timezone
30-minute consultation
Brief but comprehensive overview of our solutions
Meet our product experts
Get answers to your specific questions